Thermoforming vs. Metal Stamping
Are you trying to decide between thermoforming and metal stamping? We can help!
Learn the pros and cons of thermorming vs. metal stamping
In manufacturing, the processes of shaping materials into final products are as diverse as the products themselves. Two such pivotal processes in the manufacturing industry are thermoforming and metal stamping.
Each method has evolved, harnessing technological advancements to offer efficient and precision-based solutions for various applications. This section will introduce you to the basics of these processes, tracing their historical roots and highlighting their unique characteristics.
Thermoforming: An Overview
Thermoforming is a process primarily involved in the shaping of plastics. It involves heating a plastic sheet to a pliable forming temperature, forming a specific mold shape, and trimming it to create a usable product, typically used in or in conjunction with another product.
The journey of thermoforming as a mainstream industrial process dates back to the early 20th century. It gained significant momentum with the advent of newer and more versatile plastic materials in the mid-20th century, which opened up many applications ranging from packaging to automotive parts.
Metal Stamping: The Process and Its Evolution
Contrasting thermoforming, metal stamping is a process primarily focused on cutting and shaping metal sheets. This process involves placing flat sheet metal, in either coil or blank form, into a stamping press where a tool and die surface form the metal into a new shape. The roots of metal stamping can be traced back to the times when manual hammers and anvils were used.
However, with the Industrial Revolution and the development of complex machinery, metal stamping evolved into a high-speed, high-precision process widely used in the automotive, aerospace, and electronics industries.
While sheet metal fabrication has a similar end goal to thermoforming, the processes differ in material, method of manipulation, cost, environmental impact, and much more.
Thermoforming vs. Metal Stamping: A Comparative Look
.jpg?width=2000&height=1330&name=unnamed%20(2).jpg)
While thermoforming and metal stamping are pivotal in manufacturing, they cater to different materials and have distinct operational methodologies. Thermoforming, exclusive to plastic materials, offers versatility in shaping complex contours and is often preferred for more extensive, less detailed items.
In contrast, metal stamping is known for its precision and efficiency in handling metal sheets, making it ideal for high-volume production runs with intricate details and high structural integrity requirements.
In the following sections, we will delve deeper into the intricacies of these processes, focusing mainly on the use of plastic and metal in each method, exploring their advantages, challenges, and the implications of choosing one over the other in various manufacturing scenarios.
Material Considerations
When comparing thermoforming to metal stamping, one of the fundamental differences lies in the materials used in each process. Understanding these differences is crucial for manufacturers and designers to decide which process best suits their needs.
Thermoforming Uses Plastic, Metal Stamping Uses Metal
Thermoforming is a process that primarily uses plastic materials. It involves heating a plastic sheet until it becomes pliable, then forming it over a mold. The versatility of plastic materials makes thermoforming a preferred choice for a wide range of applications, from packaging to automotive components.
In contrast, metal stamping involves the shaping of metal sheets. This process is used extensively in industries that require high-strength components, such as automotive and aerospace. Metal stamping is known for its durability and ability to produce large quantities of parts with uniform precision.
List of Materials Available for Each Process
Thermoforming Materials:
- Acrylic (PMMA)
- Polycarbonate (PC)
- Polyethylene (PE)
- Polypropylene (PP)
- Polystyrene (PS)
- ABS (Acrylonitrile Butadiene Styrene)
Metal Stamping Materials:
- Steel (including stainless steel)
- Aluminum
- Copper
- Brass
- Nickel
- Titanium
Each of these materials has its own properties, like strength, flexibility, and resistance to heat or chemicals, which determine their suitability for different applications.
Thermoforming - Lower Material Costs
One significant advantage of thermoforming is the lower material costs compared to metal stamping. Plastic materials are generally less expensive than metals, especially considering the cost of precious or rare metals like titanium or nickel. This cost-effectiveness makes thermoforming an attractive option for projects with tight budgets or for items that require less structural integrity.
Moreover, the thermoforming process can be more cost-effective for smaller production runs. It allows for more straightforward tooling changes and shorter setup times, which is advantageous for custom or limited-edition products. On the other hand, while more cost-effective in large volumes, metal stamping can be expensive for small-batch production due to the high cost of tooling and setup.
Production Volume
Thermoforming for Low to Medium Volumes
Thermoforming is particularly suitable for low to medium production volumes. This adaptability is due to the relatively straightforward setup and changeover processes in thermoforming. It allows for efficient production of smaller quantities without incurring significant costs. This flexibility is a significant advantage for custom projects or products that do not require mass production.
Metal Stamping for High-Volume Metal Parts
Conversely, metal stamping shines in high-volume production. The process is designed to produce large quantities of metal parts quickly and consistently. Once the initial setup and tooling are complete, metal stamping machines can operate at high speeds, churning out vast numbers of identical parts. This efficiency makes metal stamping a go-to choice for industries needing high-volume, uniform metal components.
Tooling Complexity and Cost
Thermoforming: Simpler Tooling for Plastic Guides
The tooling required for thermoforming is generally less complex and, consequently, less costly. Thermoforming molds can be made from less expensive materials like wood or aluminum for lower-volume production, significantly reducing the initial investment. This aspect makes thermoforming an accessible option for smaller businesses or projects with limited budgets.
Metal Stamping: Complex Dies and Punches
In contrast, metal stamping requires more intricate and robust tooling. Dies and punches used in metal stamping are typically made from hardened steel to withstand the stamping process's high pressures and repetitive actions. The complexity and durability required for these tools result in higher initial costs, making metal stamping a more significant investment, particularly for small-scale projects.
Cost-Effectiveness
Thermoforming for Lower Volumes
Thermoforming is more cost-effective for lower production volumes. The lower tooling cost and the ability to quickly change molds make it ideal for producing a limited number of parts without a hefty investment. This cost structure suits custom orders, prototypes, and specialized products where the quantity needed does not justify the high cost of metal stamping tooling.
Metal Stamping for Higher Volumes
As production volume increases, the cost-effectiveness of metal stamping becomes more apparent. The initial high cost of creating dies and setting up production lines is offset by the low per-unit cost when producing large quantities of parts. The economies of scale make metal stamping a more financially viable option for mass-produced items.
Reduced Machining and Post-Forming Fabrication/Assembly Costs
Ease of Fabrication with Thermoforming
Thermoformed plastic parts often require minimal post-processing, which reduces additional machining and fabrication costs. The ability to mold plastic into complex shapes in a single operation can eliminate the need for multiple manufacturing steps. This simplicity saves time and reduces labor and material costs associated with additional processing.
Weight Considerations
Thermoforming Parts: Lightweight and Durable
Thermoformed parts are typically lighter than their metal counterparts, which has several advantages. The reduced weight leads to less wear on machinery and presses used in production. In industries where weight is a critical factor, such as automotive and aerospace, the lightweight nature of thermoformed parts can significantly impact performance and fuel efficiency.
Furthermore, the lighter weight of thermoformed parts facilitates easier handling and installation, which can be crucial in specific applications. This ease of handling can reduce labor costs and improve safety during assembly and installation processes.
Thermoforming and Sustainability
Addressing Concerns About Plastic Waste
Plastic waste is a significant environmental concern. Thermoforming, which predominantly uses plastics, must address these concerns proactively. Innovations in the industry focus on reducing plastic waste through efficient design and minimizing excess material use during production. In most cases, the excess materials required for the production process is reprocessed and blended with new material to be used to make additional parts using partially closed loop industrial recycling streams.
Potential for Recyclable and Eco-Friendly Plastics
The thermoforming industry is increasingly adopting recyclable and eco-friendly plastics. Biodegradable plastics and those made from renewable resources are gaining traction. Efforts are also underway to improve recycling techniques to ensure that thermoformed products have a minimal environmental footprint.
Metal and Sustainability
Metal stamping has a slight advantage in terms of recyclability. Metals like steel and aluminum can be recycled repeatedly without the degradation in quality that plastics incur This aspect makes metal stamping a more sustainable option, as it can reduce the need for new material extraction.
Environmental Impact of Metal Extraction
However, the extraction and processing of metals have a considerable environmental impact. Mining activities can lead to habitat destruction, water pollution, and greenhouse gas emissions. These factors need to be weighed when considering the overall environmental impact of metal stamping.
Industry-Specific Comparisons
.jpg?width=2000&height=1330&name=unnamed%20(2).jpg)
Packaging Industry
In the packaging industry, thermoforming is often preferred for its versatility in creating custom packaging solutions. The ability to use recyclable plastics is also a plus for sustainability. Metal stamping is less common in this industry due to the nature of packaging requirements.
Automotive/Vehicle Interior Components
Thermoforming and metal stamping have their places for automotive and vehicle interiors. Thermoforming is used for lighter, aesthetic components, while metal stamping is essential for structural parts. The choice between the two often depends on the specific application and weight considerations. Automotive engineers continue pushing the envelope on replacing metals with plastics for vehicle weight reduction.
Electric Vehicles/Batteries
Thermoforming and metal stamping are crucial in the rapidly growing electric vehicle (EV) sector, particularly in battery technology. Thermoforming can insulate components and casings, while metal stamping is integral in creating durable, conductive parts for EV batteries. The lower volumes of EV continues to be attracted to thermoforming to keep startup costs low during product development.
Conclusion
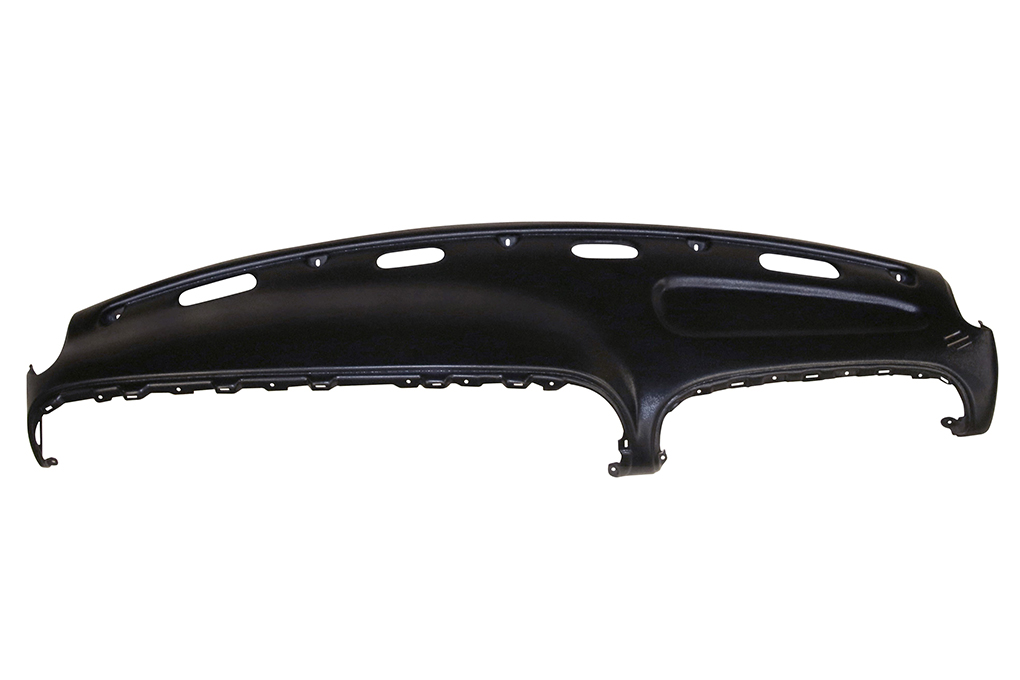
The decision to use thermoforming or metal stamping depends on many factors. These include production volume, material requirements, industry specifications, cost considerations, and environmental impact. While thermoforming offers flexibility and lower costs for lower volumes, metal stamping stands out for its durability and efficiency in high-volume production.
Environmental considerations also play a crucial role, with the sustainability of materials and processes becoming increasingly important. Advances in recyclable plastics and efficient metal recycling processes are shaping the future of these industries.
Ultimately, the choice between thermoforming and metal stamping is not a matter of one being superior to the other but instead finding the right fit based on the specific requirements of a project or application.